Discover How To Ensure Quality In Apparel Manufacturing with expert strategies on fabric selection, production processes, and quality control techniques. Learn how to maintain high standards, minimize defects, and enhance efficiency in garment production. From raw materials to final inspection, ensure excellence at every stage. Elevate your brand with top-tier quality assurance practices. Read more to master the art of premium apparel manufacturing!
Thank you for reading this post, don't forget to subscribe!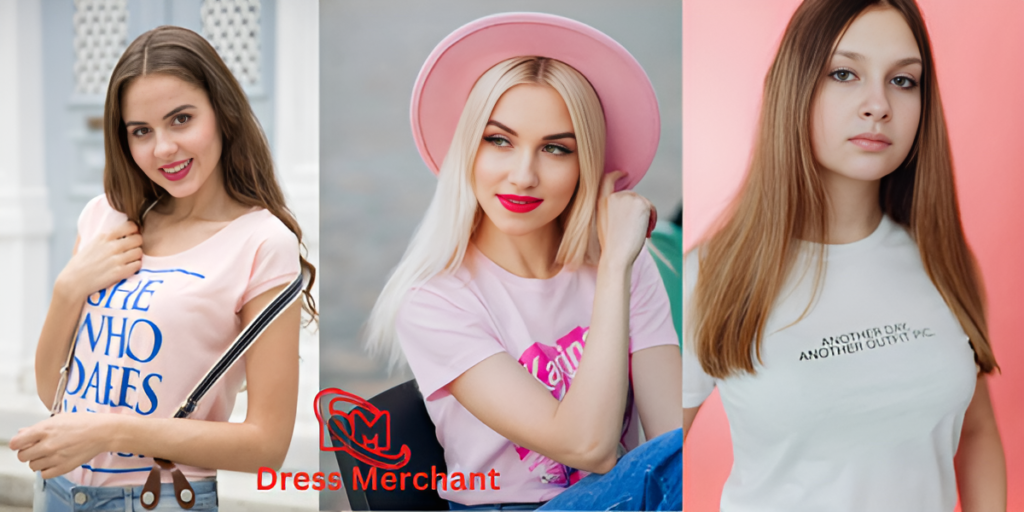
1. Selecting High-Quality Raw Materials
The foundation of a high-quality garment begins with premium raw materials. Every component, from fabric to trims, plays a crucial role in the final product’s durability, comfort, and aesthetics. By carefully selecting the best materials, manufacturers can ensure superior product quality, longevity, and customer satisfaction.
Factors to Consider When Choosing Raw Materials:
- Fabric Quality: Evaluate fiber composition, thread count, tensile strength, and shrinkage properties to determine durability and comfort. High-quality fibers such as organic cotton, merino wool, and bamboo fabric enhance breathability and longevity.
- Color Fastness: Ensure that the fabric retains color even after multiple washes, exposure to sunlight, and friction. Testing for washing, rubbing, and perspiration resistance helps prevent fading.
- Durability: Opt for materials that withstand wear and tear, ensuring the garment maintains its shape, texture, and appearance over time. Fabrics with reinforced weaves or blends like polyester-cotton offer enhanced durability.
- Compliance Standards: Choose materials that adhere to international quality and environmental certifications such as OEKO-TEX, GOTS (Global Organic Textile Standard), and Bluesign. These certifications ensure the fabric is free from harmful chemicals.
- Supplier Reliability: Source materials from trusted vendors with a track record of quality assurance and ethical sourcing. Conduct regular audits to verify consistency in raw material quality.
By prioritizing high-quality raw materials, manufacturers can reduce defects, enhance the feel and performance of their garments, and meet stringent industry standards.
2. Implementing Standardized Production Processes
A well-defined and standardized production process ensures consistency, efficiency, and reliability in garment manufacturing. By implementing structured workflows and best practices, manufacturers can minimize variations and achieve uniform product quality.
Key Steps in Standardizing Production:
- Developing Standard Operating Procedures (SOPs): Document every stage of production, from fabric inspection to final packaging, ensuring clear guidelines for workers.
- Process Automation: Invest in automated cutting, stitching, and finishing machines to enhance precision and reduce human error.
- Training and Skill Development: Regular training programs equip workers with the necessary skills to adhere to standardized procedures and improve workmanship.
- Production Workflow Optimization: Streamline operations to eliminate bottlenecks, reduce lead times, and enhance productivity. Implement lean manufacturing principles to optimize efficiency.
- Regular Monitoring: Conduct periodic audits and process reviews to identify inefficiencies and implement improvements.
A standardized production approach leads to higher output quality, reduced production costs, and improved customer satisfaction.
3. Quality Control at Every Stage of Manufacturing
Quality control (QC) is crucial to ensuring that every garment meets established quality standards before reaching the market. Implementing strict QC measures at each stage of production minimizes defects and enhances overall product quality.
Key Quality Control Measures:
- Pre-Production Quality Check: Inspect raw materials, prototypes, and initial samples for compliance with specifications before full-scale production begins.
- In-Process Quality Control: Conduct quality checks during cutting, sewing, and finishing to identify and rectify issues early in the production cycle.
- Post-Production Inspection: Evaluate final garments for stitching consistency, sizing accuracy, and aesthetic appeal before packaging.
- Random Sampling & Testing: Select random garments from each batch to verify uniformity and adherence to design specifications.
- Third-Party Audits: Engage external inspection agencies to ensure compliance with global quality standards and industry best practices.
A rigorous QC system reduces product recalls, enhances brand reputation, and boosts customer confidence.
4. Ensuring Precise Pattern Making and Cutting
Accurate pattern making and cutting are essential for achieving a consistent garment fit and structure. Even minor errors in these processes can lead to sizing inconsistencies and fabric wastage.
Best Practices for Pattern Making and Cutting:
- Use CAD Technology: Leverage computer-aided design (CAD) software for precise and scalable pattern creation, reducing manual errors.
- Check Pattern Grading: Ensure that size variations are correctly proportioned across different size ranges to maintain fit accuracy.
- Precision Cutting Techniques: Utilize laser cutting or automatic cutting machines to enhance precision and reduce material wastage.
- Lay Planning Optimization: Arrange fabric layers strategically to maximize efficiency and minimize leftover material.
- Frequent Quality Checks: Regularly inspect cut fabric pieces to prevent defects before assembly.
By focusing on precision in these early stages, manufacturers can improve garment fit, reduce production waste, and enhance overall efficiency.
5. Implementing Stringent Sewing Standards
Sewing is one of the most critical stages in garment manufacturing. Proper stitching techniques, thread selection, and machine maintenance directly impact the garment’s durability and finish.
Essential Sewing Quality Control Measures:
- Use High-Quality Thread: Ensure the thread’s strength, elasticity, and colorfastness align with garment requirements.
- Monitor Stitch Density: Maintain optimal stitches per inch (SPI) for strength and flexibility without compromising fabric integrity.
- Ensure Seam Reinforcement: Apply bar tacking, overlocking, or double stitching in high-stress areas to prevent seam failure.
- Regular Machine Maintenance: Keep sewing machines well-maintained to prevent skipped stitches, tension issues, or mechanical faults.
- Standardized Stitching Techniques: Train sewing operators to follow consistent stitching methods for uniformity and professional finishing.
A well-executed sewing process ensures garments are durable, comfortable, and visually appealing.
6. Conducting Comprehensive Fabric Testing
Fabric testing is essential to ensure textiles meet industry standards for strength, durability, and safety. Conducting pre-production fabric tests helps detect potential issues before full-scale manufacturing begins.
Common Fabric Tests:
- Shrinkage Test: Determines how much fabric contracts after washing and drying.
- Tensile Strength Test: Evaluates fabric resistance to stretching and tearing forces.
- Pilling Resistance Test: Measures the fabric’s ability to resist surface fuzz formation.
- Colorfastness Test: Assesses how well fabric retains color under washing, friction, and sunlight exposure.
- Moisture Management Test: Tests the fabric’s ability to wick sweat and maintain comfort during wear.
By implementing fabric testing protocols, manufacturers can ensure that garments maintain their structure, appearance, and performance over time.
7. Adhering to Global Compliance and Sustainability Standards
Meeting international quality and sustainability standards is crucial for credibility and market expansion. Ethical production practices also enhance brand reputation.
Important Industry Standards:
- ISO 9001: Quality management system certification.
- OEKO-TEX Standard 100: Certifies that fabrics are free from harmful substances.
- GOTS (Global Organic Textile Standard): Certification for organic fiber textiles.
- Fair Trade Certification: Ensures ethical labor practices and fair wages.
- SA8000: Social accountability certification for fair working conditions.
Compliance with these standards ensures responsible production and enhances marketability.
8. Implementing Lean Manufacturing for Quality Optimization
Lean manufacturing reduces waste, optimizes efficiency, and improves overall product quality.
Key Lean Manufacturing Principles:
- Just-in-Time (JIT) Production: Minimizes overproduction and storage costs.
- Continuous Improvement (Kaizen): Encourages ongoing process enhancements.
- Root Cause Analysis: Identifies and resolves defects at the source.
- Employee Involvement: Engages workers in quality improvement initiatives.
- 5S Methodology: Organizes workstations for optimal efficiency and safety.
Implementing lean practices ensures high-quality production while reducing costs and environmental impact.
Conclusion: How To Ensure Quality In Apparel Manufacturing
Ensuring quality in apparel manufacturing is a multi-faceted and dynamic process that requires meticulous attention to every stage of production, from raw material selection to the final inspection. Each step plays a crucial role in determining the overall durability, comfort, and aesthetic appeal of the finished product.
By implementing robust and standardized quality control measures, manufacturers can detect and rectify defects early, reducing waste and enhancing efficiency. Maintaining compliance with global industry standards—such as ISO, OEKO-TEX, and GOTS—ensures that garments meet regulatory and ethical guidelines, making them more competitive in international markets.
Additionally, investing in skilled labor and advanced technology contributes significantly to superior craftsmanship and production efficiency. Skilled workers bring expertise and precision, while modern machinery and automation enhance accuracy and consistency in fabric cutting, stitching, and finishing. Ultimately, a proactive approach to quality assurance fosters customer satisfaction, builds brand reputation, and promotes long-term business growth. In an industry driven by ever-changing trends and consumer expectations, apparel manufacturers who prioritize quality and innovation will continue to thrive in the competitive global marketplace.